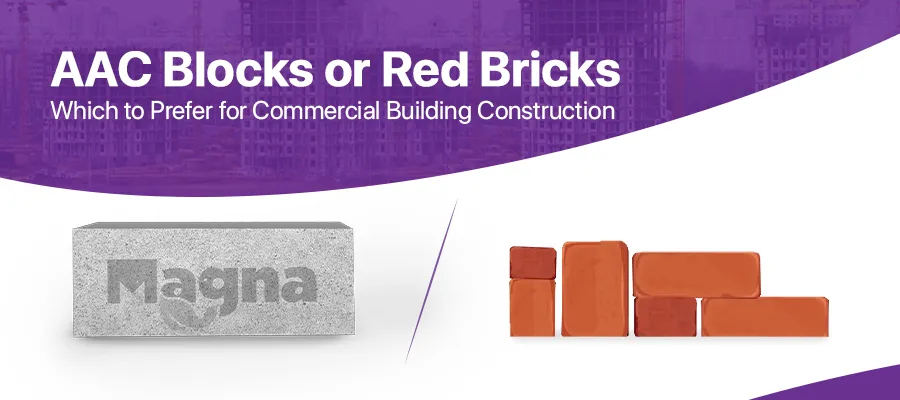
AAC Blocks or Red Bricks, Which to Prefer for Commercial Building Construction
The construction industry is experiencing a great shift in the domestic and international markets. AAC Blocks have attracted people's attention and influenced their preferences for building materials.
Technical properties are the foremost criterion in selecting construction materials. The transition is gradual and consistent.
AAC Blocks meet the requirements to construct a building. Commercial construction is the niche sector where the AAC Blocks have completely replaced the utilization of red bricks.
Reduced Investment
Cost-effective construction can be achieved from the construction materials preferred in the complete structural development.
Commercial building structures are constructed in larger floor areas. Hence, the consumption of resources will be in huge volume.
It is said that the time involved in constructing columns and beams is lesser than in constructing wall structures. When it comes to red bricks, the estimated volume of bricks is greater, which reflects in adding to the project's overall cost.
AAC Blocks has the leverage of reducing the project construction cost and time.
Hassle-Free Construction
A single AAC Block equals the cumulative dimension of 3 Red Bricks. Constructing a commercial building with AAC Blocks limits resource allocation to the greatest extent.
The space required for stacking AAC Blocks is less, which is not the same case with Red Bricks.
Space constraint becomes the barrier to constructing the commercial building where the site is located in heavy traffic or busy zone. With AAC Blocks, the number of times in stacking can be limited. Hassle-free construction is assured through AAC Blocks.
The delay or insufficient material stacking leads to inefficient construction. The pause and resuming of construction work results in project loss.
The advantage of concrete blocks is that larger dimensions reduce the special space allocated for uninterrupted construction.
Curing and Project Delivery
Commercial buildings are greater in height and larger in floor dimensions. The concrete structure has to be erected floor by floor.
The curing comes to deliver its significance in quality construction. The wall structures can be constructed with AAC Blocks or Red Bricks. The curing time is longer when wall construction is carried out with Red Bricks.
Hence the project completion exceeds the estimated time. This is not the same case with AAC Blocks.
Reason? The AAC Blocks manufacturing follows the curing process before the blocks are ready-to-use.
Therefore the time required for wall construction is lesser. AAC Blocks outperform the red bricks in curing factors.
Raising floors in a multi-story commercial building can be achieved within the estimated time.
Uniformity Adds Value
Uniform size, dimension, and weight are the critical factors influencing the effectiveness of a brick/block. AAC Blocks meet these criteria.
Consistency cannot be achieved when it comes to Red Bricks, and compromising any of the factors is common. The structural design becomes complex when constructed with uneven brick size and weight.
The under or over-burning of red bricks reflects on the varying technical properties of the bricks. The load transfer differs, resulting in varying load calculations. Hence, the life expectancy and serviceability of the commercial building are less compared to the estimated time.
AAC Blocks are manufactured in-house. It adds value to manufacturing blocks of uniform size and even weight.
The load transfer calculations can be made precise. Hence, quality construction is assured. Thereby, the building is suitable to use for the calculated life expectancy period.
These factors are essential for constructing commercial buildings
Reduced Dead Load
Wall Structure contributes to the addition of dead load in the building structure. Every structural engineer aims to reduce dead load to the maximum possible limit.
Compared to red bricks, AAC Blocks share less dead load. In other words, concrete blocks are lightweight.
The structural elements and reinforcement requirements at various construction points can be optimized. Hence, reducing resource consumption results in cost-effectiveness.
In addition, as the blocks are larger in dimensions, faster construction of wall structures and reduced mason requirements can be achieved.
But red bricks are smaller in dimension. Hence, the erection of wall structure incurs more time and masons. The more volume adds a higher dead load to the commercial building structure.
AAC Blocks make construction and structural engineering simpler.
Resistance to Climatic Changes
High-rise commercial buildings are typically subjected to high exposure to environmental conditions. The climatic changes of summer and monsoon affect the building's life expectancy. Red bricks have high water absorption properties.
During the monsoon season, the wall structure absorbs the moisture content. As a result, the wall becomes weak and incurs irregular maintenance.
Also, in the summertime, the red bricks absorb the hot outdoor temperature, making a living in the building challenging. AAC Blocks have the best advantage over red bricks in monsoon and summer climatic conditions.
Concrete blocks have low water absorption and high resistance to thermal. Hence, living in a building constructed with AAC Blocks is better than the red bricks.
Conclusion
AAC Blocks will be the most preferred choice in constructing commercial buildings. AAC Blocks outperform every critical factor that influences building quality. In addition, Concrete Blocks are cost-effective compared to Red Bricks. If you're looking to procure the best AAC Blocks, Magna Green Building Materials will be your one-stop solution to fulfil your requirements. Please visit https://www.magnagreen.in/aac-blocks for more information.